When you spend the time and money to have an epoxy or urethane floor coating installed at your facility, you expect it to work well and last for years to come. So the last thing you want to see just a few weeks after the process is done is widespread bubbles or blisters in the surface of the coating!
Unfortunately, the formation of blisters and bubbles in an industrial floor coating is a fairly common problem. Below we’ll look at the causes and find out how to prevent these issues.
Causes of floor coating blisters
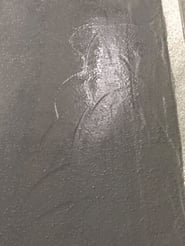
While blisters and bubbles may look similar (they’re unsightly either way!), their causes are quite different. Blistering is osmotic — a coated surface continually exposed to water or high humidity is most likely to show blistering. The source of the moisture might be the concrete itself—water vapor may be coming up through the porous concrete from the ground or as part of the curing process.
Contamination by water-soluble salts or solvents, or temperature differences across the coating surface during application can also add to the risk of blistering damage.
Causes of floor coating bubbles
Bubbling typically is not the result of water damage, but environmental or substrate problems, particularly during the drying or curing process.
For example, if a floor coating is applied to concrete on a sunny day and sunlight shines directly on the coating while it dries, the top layers will dry faster than those closer to the substrate, leading to bubbling when the uneven temperatures meet.
Other problems that may cause bubbling include:
- Flooring that is too porous for your chosen floor coating
- Temperatures that are outside the recommended range during application
- Extra-thick application of the coating layers that causes uneven curing
Preventative steps
As the old saying goes, an ounce of prevention is worth a pound of cure. Before getting a crew to apply your floor coating, you’ll want to have a flooring expert inspect your facility and notify you of any environmental factors that may affect your new floor coating.
For example, you’ll want to get a professional moisture test completed on your concrete to determine whether a moisture vapor barrier is needed to prevent blistering.
Once your building has been assessed, you’ll want to make sure to hire an experienced installation crew who will take the proper steps to properly clean and prepare the floor to ensure the coating bonds correctly and maximizes its effectiveness.
What if my floor has already been damaged?
Blistering and bubbling in the surface of a floor coating may be a functional problem that requires immediate reapplication or repair. Sometimes, however, the problem is simply an aesthetic one. While most bubbling or blistering will require some kind of solution, you may find that your floor coating is able to last for its expected lifespan.
Check to see if the structure of the coating is broken by the bubbling or remains intact. If it does not fracture, you may not need to worry. However, you’ll want to call in a floor coating specialist to advise you on what the best option is for your facility.
Need a floor coating specialist?
CPC Floor Coatings works hard to ensure that blistering and bubbling for a new floor coating is kept to an absolute minimum. We provide inspections on-site so we know exactly what kind of substrate we’re working with and what the job will require.
If you manage a commercial or industrial facility in the Southeastern U.S., contact one of our flooring experts for a free consultation. We’d love to help you get the most out of your new industrial floor coating!