Are you an industrial facilities manager approaching the end of your company’s fiscal year? Do you need to use up an expiring maintenance budget, but don’t want to fall into the trap of wasting money on low-value projects?
If your facility doesn’t currently have pressing or high-priority repair needs, now’s the time to invest in preventative maintenance. If your building has a concrete floor, this is a great place to focus on.
Here are five reasons investing in concrete polishing or an industrial floor coating now can pay dividends in the year to come:
1. The right treatment can proactively protect your floor from long-term damage
Concrete is a remarkably durable building material, but it’s not indestructible. As it ages, concrete is prone to cracking, spalling, staining, and shedding. Treating your floors for the first time or replacing an old coating can go a long way in protecting the underlying structure.
The process of polishing concrete actually increases the density of the floor, making it better able to withstand heavy loads. An industrial floor coating such as epoxy or urethane can protect the floor from abrasions and even prevent cracking in case of heavy impact. Coatings can also prevent staining by keeping liquids on the surface of the floor instead of seeping into the porous concrete beneath.
2. Minor floor damage can worsen dramatically over a year
If you’ve noticed your floor has large cracks, uneven surfaces, or a little bit of chipping or spalling starting, you don’t want to put off repairs. An area with spalling can quickly spread, especially if it’s in an area of heavy machinery or foot traffic. Damaged or uneven floors also cause other maintenance issues, such as difficulty cleaning or increased wear-and-tear on equipment. Learn more about the problems caused by damaged concrete floors.
3. Poorly maintained floors can cause worker health & safety issues.
It’s not hard to see how damaged or uneven concrete can cause tripping hazards for your employees. But there are other risks that a poorly maintained floor can pose as well. If your employees regularly drive forklifts or other vehicles over the floor, the constant jarring can actually contribute to operator fatigue, and may even aggravate back conditions. In facilities that handle chemical or organic substances, occasional spills can result in contaminated air quality and possible respiratory problems, since it’s very difficult to remove a liquid that’s seeped deep down into the porous concrete and harboring the growth of mold or bacteria.
4. Poorly maintained floors can impact employee morale
It should be obvious that an ugly or poorly maintained floor will affect the way a customer views your business. But what about your employees? Granted, someone who works in a manufacturing or warehouse environment probably isn’t expecting the floor to be beautiful, but a damaged or stained floor that isn’t repaired can make the whole facility feel a little run-down. It can also communicate that managers don’t care about details, so why should employees?
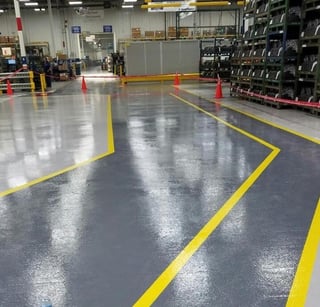
5. A well-thought-out floor design can actually improve efficiency
Investing in your floor can do more than just prevent problems. With proactive planning and an expert eye, you can use floor stripes and marking to implement a better organization system (we recommend the 5S methodology) and control traffic flow. Read more about how floor striping can improve efficiency in your facility.
Get the most out of your investment
As we explained in our post about how much industrial flooring should cost, the cost of a concrete floor maintenance project can vary depending on the size of your facility and the services you need. In order to make sure you’re getting good value out of your budget, we recommend getting estimates from several professional contractors. Once you have the numbers, don’t just go with the lowest bidder—consider how each handles your questions, and which seems to offer the most value per dollar.
If you’re in the Southeastern U.S., CPC Floor Coatings would be happy to talk with you about the details your project and provide you with a free estimate. Call us at (864) 855-0600 or fill out our online form to request a consultation.